Автор: ГалинаРаздел: Анализ микроструктуры материалов
Автор: ГалинаРаздел: Анализ микроструктуры материалов
Автор: Раздел: Атомно-силовая микроскопия
Автор: ГалинаРаздел: Анализ микроструктуры материалов
Автор: ВикторРаздел: Атомно-силовая микроскопия
Автор: ВикторРаздел: Атомно-силовая микроскопия
Автор: ВикторРаздел: Атомно-силовая микроскопия
Автор: ГалинаРаздел: Анализ микроструктуры материалов
Автор: ГалинаРаздел: Анализ микроструктуры материалов
Автор: ВикторРаздел: Анализ микроструктуры материалов
Нажимая кнопку «Подписаться», вы принимаете условия «Соглашения на обработку персональных данных».
Анализ кремниевых подложек диаметром 300 мм на наличие дефектов после травления с помощью технологии ADR АСМ компании Park Systems
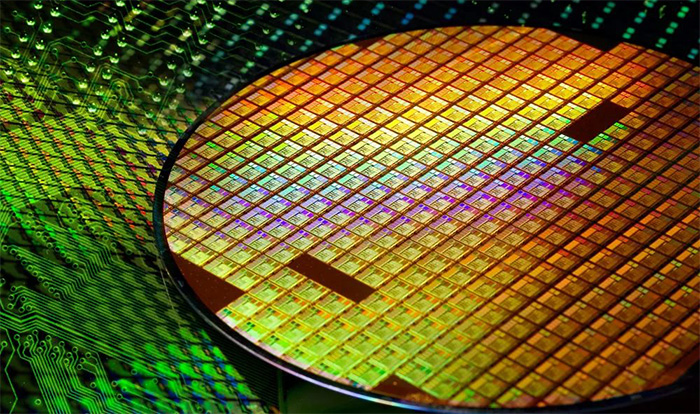
Подложки из монокристаллического кремния являются важным элементом в полупроводниковой промышленности. При изготовлении подложек методом Чохральского получаются высококачественные монокристаллические структуры с определенными дефектами, которые формируются в процессе роста кристалла или при дальнейшей обработке. Тогда как большинство дефектов могут оказывать отрицательное воздействие на производительность электронных устройств, некоторые дефекты, такие как кристаллизация осаждающихся оксидов, могут оказывать как положительное, так и отрицательное воздействие на конечный продукт.
Анализ данных дефектов может производиться за счет технологий рассеяния света на них. Однако из-за некоторых ограничений (например, большая длина волны источника света) большинство дефектов либо очень сложно, либо вовсе невозможно обнаружить. Следовательно, точной анализ формы и размеров дефектов является основополагающим при их обнаружении и классификации.
Атомно-силовая микроскопия (АСМ), в отличие от электронной сканирующей микроскопии (SEM), которая позволяет получать двумерные изображения, предоставляет возможность получать трехмерные изображения очень высокого разрешения, поскольку обладает самой высокой чувствительностью вдоль вертикальной оси сканирования[1]. Однако, такие аспекты как низкая пропускная способность, ограниченный срок службы кантилеверов и кропотливость работы для определения координат дефектов, стали камнем преткновения данной технологии для анализа дефектов больших подложек (диаметром до 300 мм).
Чтобы преодолеть вышеописанные трудности была разработана технология автоматического обнаружения дефектов (ADR) [2]. В данной статье описывается процесс измерений дефектов на подложке диаметром 300 мм, которая была подвержена тщательному процессу травления с помощью кислоты в газообразном состоянии таким образом, чтобы образовавшиеся дефекты было возможно исследовать с помощью технологии рассеяния лазерного излучения (LLS) [3].
За счет контролируемого травления дефекты образовали мелкую структуру и их распределение и относительные размеры определялись с помощью рассеяния на них лазерного излучения. Однако размеры некоторых дефектов были определены неточно из-за их очень мелкой глубины и, как следствие, слабого эффекта рассеяния.
Аналогичная ситуация была при исследовании данных дефектов с помощью SEM. Для того чтобы получить точную информацию о положении и размерах дефектов была использована технология ADR. В таком случае используется бесконтактный режим получения изображения. Этот режим является неразрушающим, что сохраняет целостность образца и кантилевера, увеличивая срок службы и производительность последнего. В итоге были получены изображения дефектов, которые затем сравнили с SEM-изображениями.
Причины использования ADR
Поскольку в данное время имеется направленность к сокращению размеров интегральных устройств, то требования по контролю их качества становятся все более жесткими. Анализ кремниевых подложек на наличие дефектов преимущественно осуществляется путем измерения разницы интенсивностей рассеянного лазерного излучения от эталонной поверхности и дефектной поверхности. Действительная степень дефектности поверхности может определяться наличием посторонних частиц, топографическими дефектами или кристаллической неоднородностью. Чтобы снизить число дефектов, необходимо знать их источник. Анализ с помощью рассеяния лазерного излучения позволяет определять только степень дефектности и примерный размер самих дефектов. Поэтому необходимо использовать АСМ для определения природы происхождения дефектов.
В данном исследовании внимание сконцентрировано на малых кристаллических неоднородностях, которые сложно обнаружить стандартными методами. Полный анализ дефектов может быть выполнен только при точной передаче данных о координатах дефектов между аналитическими инструментами. Ниже описан процесс обнаружения и анализа дефектов с помощью Атомно силовых микроскопов компании Park Systems.
Эксперимент
Процесс использования ADR на АСМ представлен на рисунке ниже. Для получения изображения важно было соблюдать два фактора:
- Точная взаимосвязь между ADR и LLS для минимизации ошибок позиционирования
- Бесконтактный режим измерения
Рис. 1. Процесс использования технологии ADR. После того, как получена координатная карта дефектов, АСМ автоматически произведет осмотр, выберет дефект, получит увеличенное изображение и произведет его анализ с последующей классификацией.
Настройка координат
Настройка координат необходима для правильного построения взаимосвязи по передаче данных между ADR и LLS. В случае неразмеченных подложек будет отсутствовать опорная точка для выравнивания. Чтобы не допустить этого, выполняется грубое выравнивание, а затем точное выравнивание. При грубом выравнивании выбираются три случайных опорных точи, чтобы скорректировать ошибки поворота и передачи. Далее выполняется точное выравнивание, чтобы исключить ошибки позиционирования, вызванные применением двух разных технологий (ADR и LLS). Несколько крупных дефектов с хорошо известными координатами используются при точном выравнивании. Так как дефекты трудно различимы при использовании стандартной оптики на АСМ, используется улучшенная оптика для обнаружения дефектов, которые далее принимаются в качестве опорных. После выравнивания образца с помощью ADR можно точно определить остальные дефекты [2].
Улучшенная оптика
Улучшенная оптика используется во время точного выравнивания, чтобы определить местоположение дефектов, исследуемых с помощью ADR технологии. Технология обнаружения основана на дифференциальном усреднении кадра изображения исследуемой поверхности в двух различных местах. Так как АСМ компании Park Systems используют независимые XY и Z сканеры (технология была разработана компанией, чтобы устранить появление перекрестных помех и, как следствие, искривление получаемого изображения), образец можно перемещать с очень высокой точностью [2]. XY сканер перемещает образец, тогда как Z сканер перемещает сам кантилевер. С помощью использования улучшенной оптики и независимых сканеров, получают два изображения поверхности в двух абсолютно разных местах, а конечное изображение получается за счет определения разницы между полученными изображениями.
Таким образом, финальное изображение обладает очень высоким контрастом, что нелегко получить при использовании обычной оптики. Ниже представлены изображения, полученные с помощью обычной оптики и улучшенной оптики.
Рис. 2. Обычное (слева) и улучшенное (справа) изображение небольшого дефекта кремниевой подложки.
В нижних правых углах показано увеличенное изображение дефекта. Видно, что при использовании улучшенной оптики дефект легко наблюдается и без дополнительного увеличения (размер всего изображения 550 × 413 мкм).
Бесконтактный режим
Бесконтактный режим – это стандартный режим в получении изображений на АСМ Park Systems. Очень важно сохранять остроту кантилевера в процессе анализа дефектов. Помимо экономии денежных средств, данный режим гарантирует постоянство качества и точности получаемых изображений от измерения к измерению. Также данный режим позволяет производить измерения в автоматическом режиме, увеличивая общую производительность. В данном режиме кантилевер колеблется на определенной резонансной частоте. Затем он подводится к поверхности исследуемого образца, в результате чего амплитуда колебаний уменьшается из-за действия сил Ван-дер-Ваальса. АСМ регистрирует данные изменения и за счет механизма обратной связи сохраняет резонансную частоту неизменной, чтобы кантилевер не задевал поверхность образца. Так как кантилевер исследует поверхность образца, Z сканер перемещает его вверх и вниз для сохранения определенной амплитуды колебаний [4]. Помимо данного режима в АСМ могут использоваться и другие режимы сканирования (контактный, динамический, латеральный и пр.)
Автоматическое обнаружение дефектов и получение изображения
Значительные улучшения в пропускной способности при анализе дефектов достигнуты благодаря использованию режима ADR, так как это полностью автоматический процесс. После того, как координаты дефектов, обнаруженные с помощью LLS, переданы на АСМ и произведено выравнивание координат, начинается обнаружение дефектов на АСМ и получение их изображений. Процесс обнаружения и получения изображений полностью автоматизирован. Автоматизация включает в себя: обнаружение дефекта, подвод кантилевера к образцу, оптимизацию параметров бесконтактного режима, проведение обзорного сканирования, оптимизацию размера получаемого изображения, итоговое сканирование, обработку данных и классификацию дефектов («выступ» или «яма»). Обычно дефекты обнаруживаются в пределах ± 10 мкм по отношению к координатам, полученным с помощью LLS.
Подготовка образца
Кремниевая подложка диаметром 300 мм вытравливалась газообразной кислотой в разряженном воздухе при температуре на протяжении длительного времени для образования на ней кристаллических дефектов[3]. Размеры и форма создаваемых дефектов зависят от исходных дефектов (см. рис. 3). После того как дефект создан, он может быть определен за счет рассеяния им излучения при использовании технологии LLS. Она позволяет определять координаты дефектов, которые затем используются SEM- и АСМ микроскопами.
Рис. 3. Схема механизма травления для создания искусственных дефектов.
Результат
Подложка была исследована с помощью LLS технологии и было выбрано 34 дефекта для анализа на АСМ с помощью ADR. Первые 21 дефект были исследованы с помощью SEM-микроскопа, прежде чем провести исследования на АСМ. Однако, изображения полученные данным методом, получаются двумерные и не дают точной информации о глубине/высоте дефекта. Остальные 13 дефектов не были обнаружены на SEM-микроскопе из-за его низкого разрешения. На рисунке ниже представлены результаты анализа дефектов с помощью SEM-микроскопа и АСМ микроскопа с функцией ADR. С помощью АСМ были найдены все 34 дефекта, обнаруженные первоначально LLS.
Рис. 4. Результаты анализа дефектов с помощью SEM и ADR (SEM и АСМ изображения дефектов повернуты на 180° по отношению друг к другу).
Анализ дефектов показал, что они принадлежат к восьми различным типам в зависимости от того, как рассеивалось излучение при LLS анализе. Временная классификация с помощью LLS основана на рассеянии дефектом излучения. Механизм рассеяния зависит от формы дефекта, его глубины/высоты и наличия центрального дефекта. Так как процесс травления искусственный, то кристаллические дефекты подвергаются вытравке с разной скоростью (в отличие от идеальной кристаллической поверхности).
Дефекты, протравленные на ранней стадии более глубокие, чем те, которые были получены позднее. Дефекты с формой перевернутой пирамиды гораздо глубже и лучше рассеивают излучение. Они были классифицированы как «фасет» (имеют плоские грани). Дефекты с искривленной формой, образовавшиеся на более поздних стадиях, были классифицированы как «поверхностные». Некоторые дефекты были вытравлены до средней степени и имели плоские грани с искривленным основанием. Такие дефекты были классифицированы как «двойного типа». Дефекты, которые успели только начать образовываться и имевшие очень слабые LLS сигналы, были классифицированы как «очень малые».
Также дефекты классифицировали по следующим признакам: имели ли они центральный дефект или нет. Таким образом, было получено восемь типов дефектов. Тип каждого отдельного вида дефекта представлен на рисунке 5. Если перемещаться по таблице (рис. 4) слева направо и сверху вниз, то можно заметить, что LLS сигнал становится слабее. Это связано с глубиной дефектов и четкостью их краев. Изображения, полученные с помощью АСМ, подтвердили разницу глубины между различными типами дефектов. Поскольку АСМ изображения несут в себе информацию о высоте, то можно использовать цветовую шкалу, чтобы охарактеризовать дефекты по глубине.
Рис. 5. Классификация дефектов по типу.
Анализ
На рисунке 6 представлено сравнение результатов, полученных с помощью SEM и АСМ для одного и того же дефекта. Первое SEM изображение представляется только в двумерном виде и поэтому появляются ограничения при определении глубины дефекта, а также изображение имеет низкую контрастность. Второе SEM изображение помогает обнаружить центр дефекта (это возможно только если сам дефект был обнаружен на первом изображении).
АСМ изображение, в отличие от SEM, дополнительно к двумерному виду содержит еще и информацию о глубине/высоте дефекта для каждого пикселя изображения. Наличие цветовой шкалы помогает отображать информацию как о высоте дефекта, так и более четко рассмотреть дефект в двумерном виде (см. рис. 5). Так как АСМ имеет самое высокое разрешение по вертикальной оси среди прочих методов анализа [1], то получаемое изображение имеет и очень высокую контрастность.
Рис. 6. Сравнение SEM и АСМ изображений.
Все 34 дефекта были обнаружены на АСМ с помощью использования технологии ADR. На рисунке ниже представлен вид дефекта, который не был обнаружен с помощью SEM микроскопа. Глубина дефекта менее 4 нм и содержит центральный дефект. Данное изображение еще раз подтверждает ограничение возможностей использования SEM микроскопов для анализа подобных дефектов.
Рис. 7. АСМ изображение дефекта №24.
Было также продемонстрировано, что АСМ использует технологию бесконтактного измерения – отсутствие разрушающего воздействия на образец и кантилевер. В отличие от АСМ, электронный пучок в SEM микроскопе может изменять поверхность образца. На рисунке 8 показаны видоизменения поверхности в результате анализа с помощью SEM (электронный пучок «сжигает» поверхность образца во время анализа). Размеры «выжженной» зоны соответствуют размеру электронного пучка. На рисунке видно, что было использовано несколько размеров пучка при попытке анализа мелкого дефекта.
Рис. 8. АСМ изображение дефекта с «выжженными» зонами от SEM.
Заключение
В данной работе были показаны возможности анализа дефектов подложек с на АСМ компании Park Systems с помощью использования технологии ADR. При использовании автоматического режима общая производительность системы увеличивается еще больше, а измерения становятся очень простыми. Атомно-силовые микроскопы компании Park Systems:
Атомно-силовой микроскоп Park NX-HDM/XE-XDM
Автоматический обзор дефектов и измерение шероховатости поверхности в доли ангстрем для сред и подложек...
Атомно-силовой микроскоп NX-/ХЕ-WAFER
Атомно-силовой микроскоп для исследования подложек с автоматической функцией оценивания дефектов...
Атомно-силовой микроскоп NX-PTR
Полностью автоматический промышленный конвейерный АСМ для, и не только, автоматизированных измерений впадины полюсного наконечника в заготовке, индивидуальной головке-слайдере, слайдерах HGA...
Атомно-силовой микроскоп ХЕ-3DM
Полностью автоматизированная система АСМ, спроектированная для измерения выступающих элементов профилей, получения боковых изображений высокого разрешения, измерений критических углов...
Ссылки
[1] G. T. Smith, Industrial Metrology: Surfaces and Roundness.: Springer, 2002.
[2] Ardavan Zandiatashbar et al., "High-throughput automatic defect review for 300mm blank wafers with atomic force microscope," in Proc. SPIE 9424, Metrology, Inspection, and Process Control for Microlithography XXIX, 2015, p. 94241X.
[3] J. Libert and L. Fei, Method to Delineate Crystal Related Defects.: PCT Publication, WO2013055368(A1).
[4] Ardavan Zandiatashbar, "Sub-angstrom roughness repeatability with tip-to-tip correlation," NanoScientific, no. Winter, pp. 14-16, 2014.
[5] Ajay Kumar and Banqiue Wu, "Extreme Ultraviolet Lithography: A Review," Journal of Vacuum Science & Technology B, pp. 1743 - 1761, 2007.
[6] James A. Folta, J. Courtney Davidson , Cindy C. Larson, Christopher C. Walton, and Patrick A. Kearney, "Advances in low-defect multilayers for EUVL mask blanks," in Proceedings of SPIE 4688, Emerging Lithographic Technologies VI, 173, 2002.